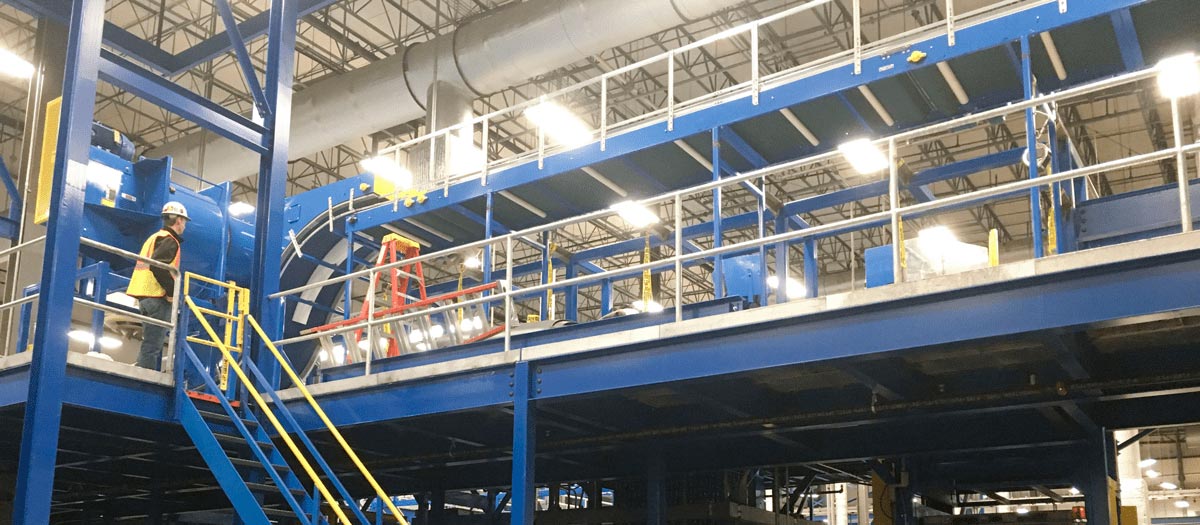
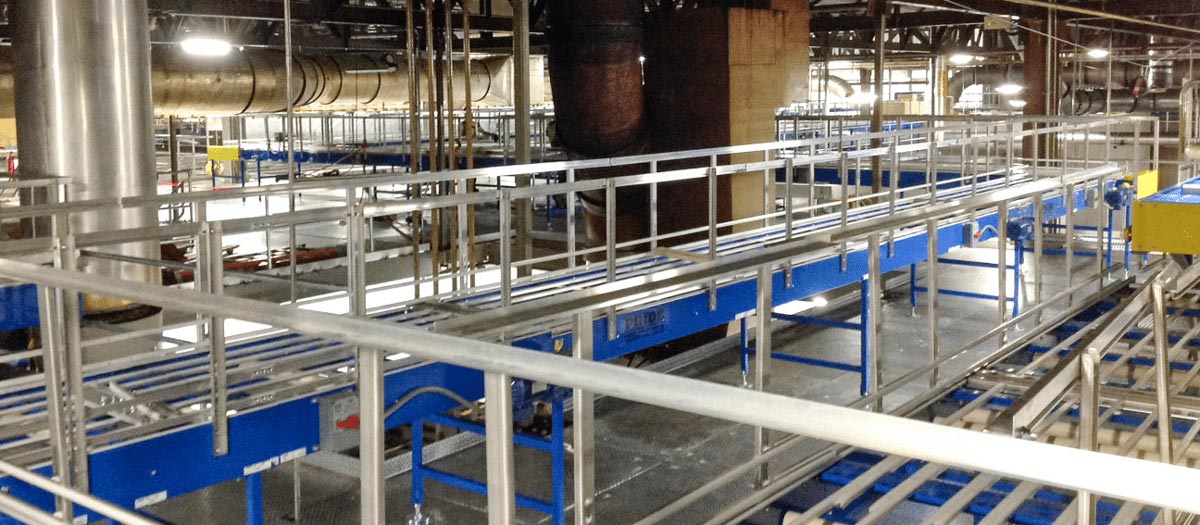
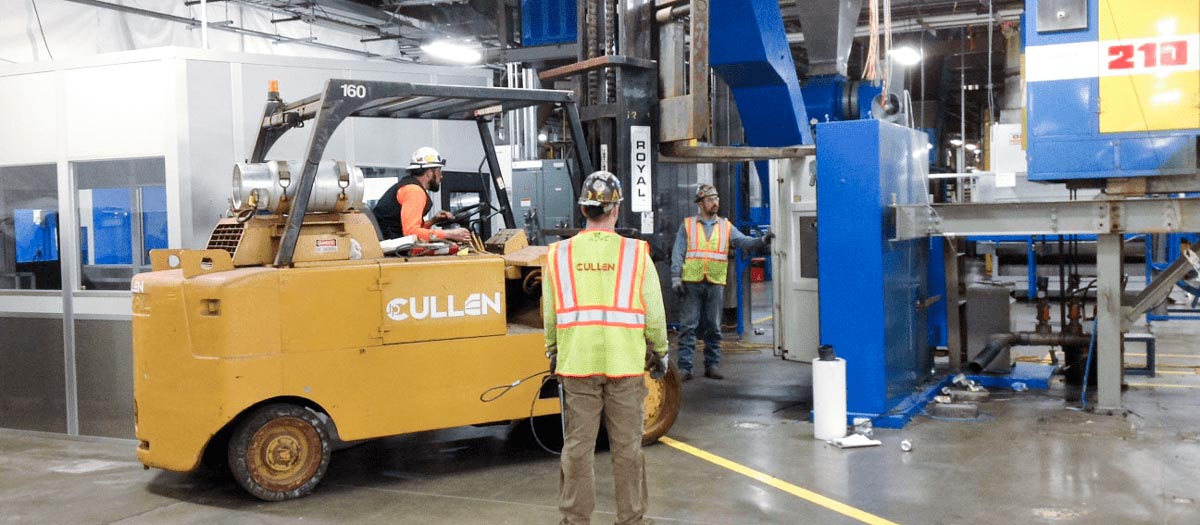
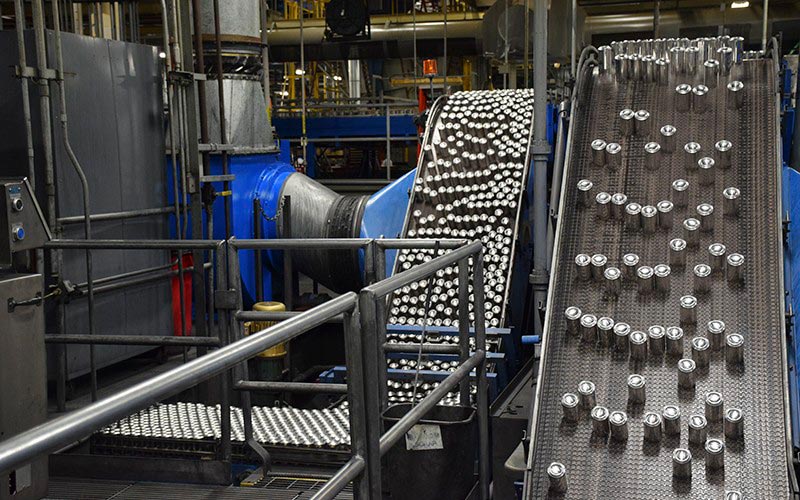
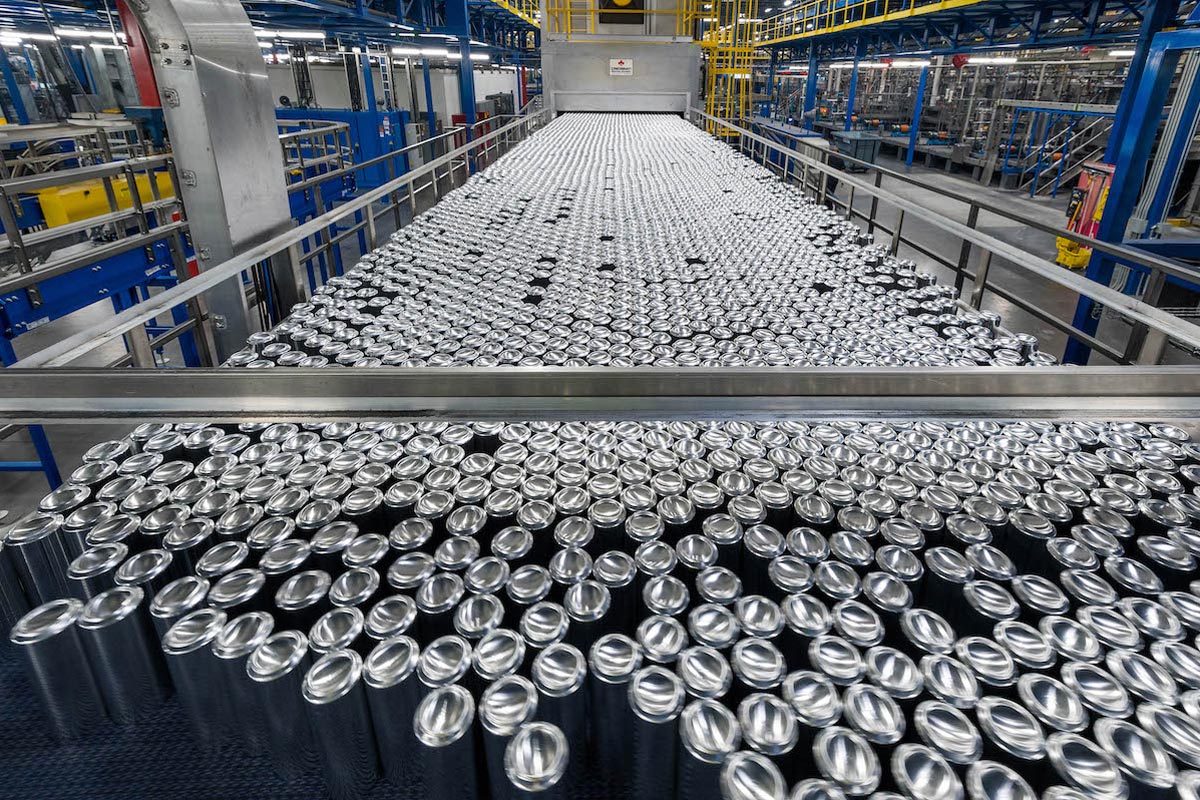
- Industrial
Ball Corporation Equipment & Conveyor Installation
Size:
Location:
Ball Corp, an aluminum can manufacturer, precisely lays out their facilities to streamline their production processes, maximizing their space, workforce, and time. To help them achieve this at their Fort Atkinson, WI facility JP Cullen performed installation of new equipment and conveyors as well as structural modifications to the existing mezzanine layout to accommodate the new equipment on (3) automated production lines.
New equipment installation frequently means production lines must be shutdown. We understand our client’s production process and the importance of getting them back up and running. It is JP Cullen’s job to plan the work so that it will be completed within, if not prior to, the end of the required shutdown period.
In addition to the challenge of installing the equipment within the aggressive shutdown period, JP Cullen also had to complete extensive mezzanine modifications to be able to work with the new equipment layout. In order to do this safely and successfully, JP Cullen’s team needed the field measurements of the existing steel to get the new structural mezzanine steel designed and fabricated in time for installation prior to the shutdown. Once the lines were shut down there would not be time to wait for steel to be fabricated. However, trusted measurements of the existing steel did not exist, and it would be next to impossible to get all of these measurements using traditional field measuring methods while the beverage can lines were operational. This presented a potentially significant road block in meeting the project shutdown schedule. During the mezzanine design, it was also determined that the steel roof trusses supporting the existing mezzanine did not have enough capacity to support the new design. JP Cullen had to act fast and develop a solid plan.
On-site laser scanning captures as-built data rapidly and precisely. This is a tool that JP Cullen has used on many of our other projects, and it provides cost-saving benefits to our clients. The JP Cullen BIM (Building Information Modeling) team scanned the existing steel, and the data was sent immediately to the steel fabricator.
With the new-found knowledge of the existing steel, JP Cullen’s steel fabricator could begin fabricating the steel and JP Cullen could begin reinforcing the trusses. This allowed the new mezzanine steel to be ready in time for the shutdown. When the shutdown started, JP Cullen was able to get to work immediately without having to wait for the new steel.
JP Cullen’s thorough efforts of pre-project planning were also vital to achieving the shutdown period. JP Cullen had the correct manpower involved and followed both the client’s safety requirements and their safety program to the letter. No accidents or necessary corrective action meant no lost time, one more way JP Cullen made sure to keep to the tight schedule.
Due to JP Cullen’s use of laser scanning and pre-planning, Ball Corp was able to get their production lines running 20% earlier than planned. In fact, each line was completed a full week earlier than originally planned according to Ball Corp’s shutdown schedule, which meant our client could begin producing cans a full week earlier on each line. JP Cullen achieved the goal we set out for: completing the job with no safety incidents, and getting Ball Corp back to producing cans ahead of schedule, ultimately saving them time and money.