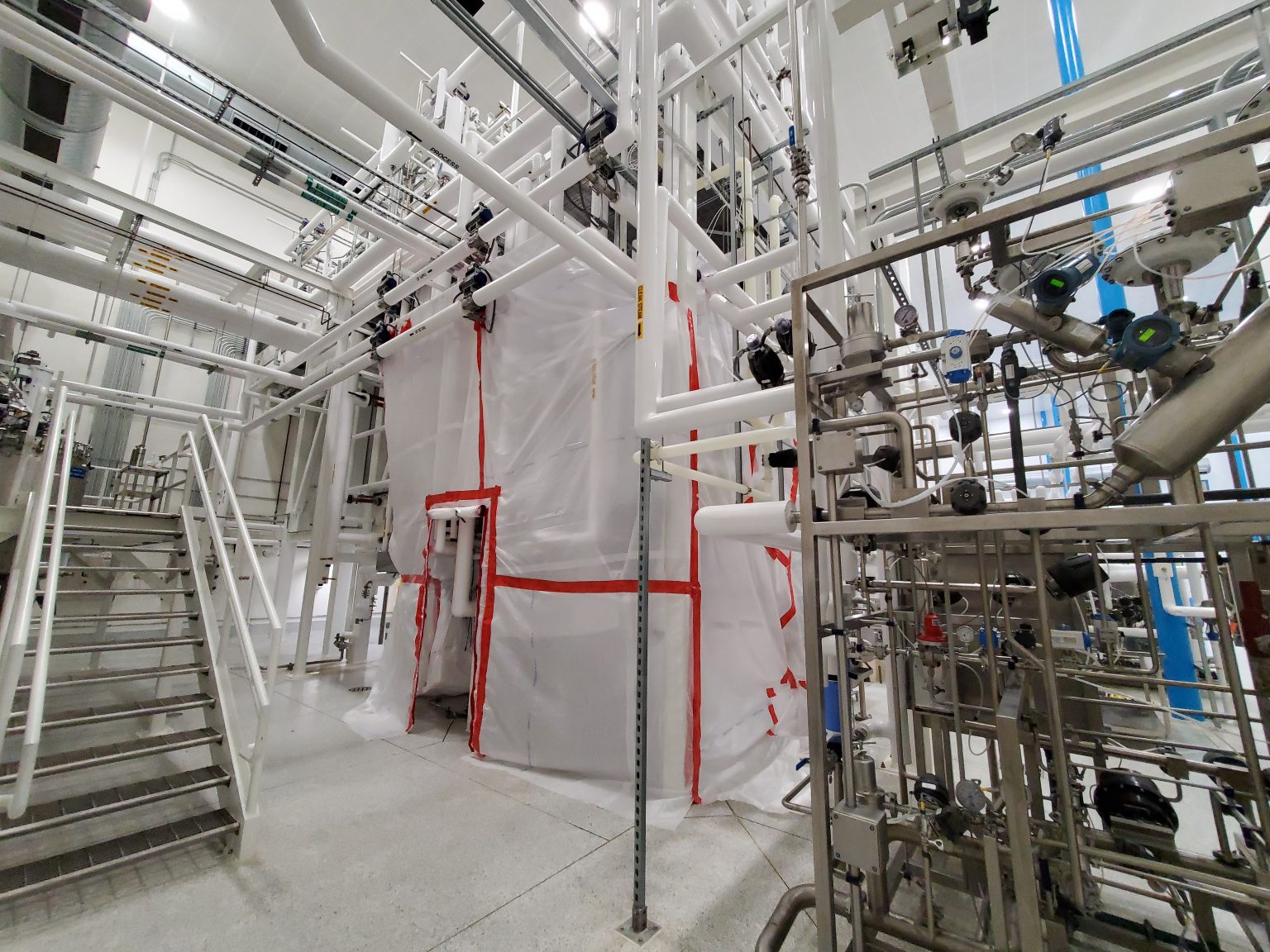
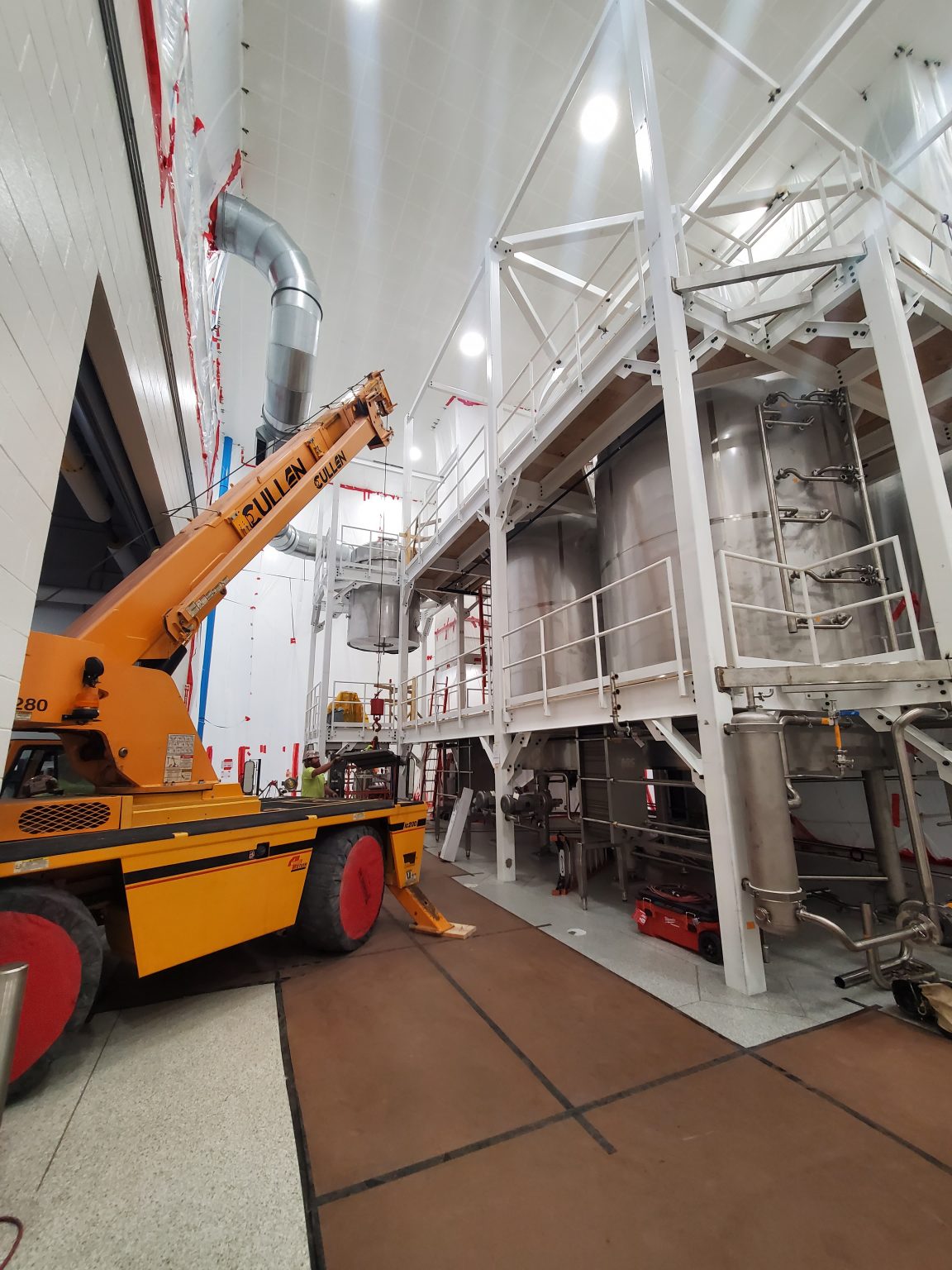
- Industrial, Science & Technology
Confidential Biotechnology Company Fermentation Expansion
- Confidential Biotechnology Company
Location:
A confidential Biotechnology company needed to increase its production capacity to meet growing demands at their facility in Southern Wisconsin where they produce probiotics for the dietary supplement market. The initiative for this project was aimed at transforming the production floor. JP Cullen was hired as the EPC to complete this project.
Our team faced a monumental challenge: installing a complete production line inside an active facility. This involved setting two large tanks, several smaller tanks and supporting process equipment next to the existing production lines. This heavy processing project required precision and expertise.
Working in an active facility meant safety and hygiene were paramount. The team had to maintain a strict barrier between the construction zone and the production areas. To achieve this, we created a containment “bubble” to prevent contamination. With ceiling elevations reaching approximately 45 feet, we erected plastic wall barriers to confine contaminants to the work area. If these barriers were to be breached, work would have to stop immediately to rectify the issue, potentially causing delays to construction as well as operations.
Our team was innovative to overcome this challenge. We used fireproof reinforced plastic, stego tape, zip ties, magnets, clamps, and straps to create a robust containment system. We also installed vents with HEPA filters and used negative air machines with turbo fans to manage pressure fluctuations. This setup ensured a stable environment within the construction zone and allowed the exterior door to be securely closed at the end of each day. Even in unfavorable weather conditions, the exterior door could be opened without compromising the facility or the strict Good Manufacturing Practices (GMP) rules. Construction and operations proceeded without any interruptions.
Another project for this facility involved replacing all the existing flow panels with valve clusters and mix proof valve manifolds. The mix proof manifolds allowed automated control for cleaning equipment with no risk of exposing product. Our team also installed a new parallel CIP circuit to increase capacity, connecting it to all existing process equipment on the current CIP loop, as well as to the new equipment from the other project. Additionally, we constructed a new maintenance access platform to provide access to process valves above the ceiling in non-production areas.