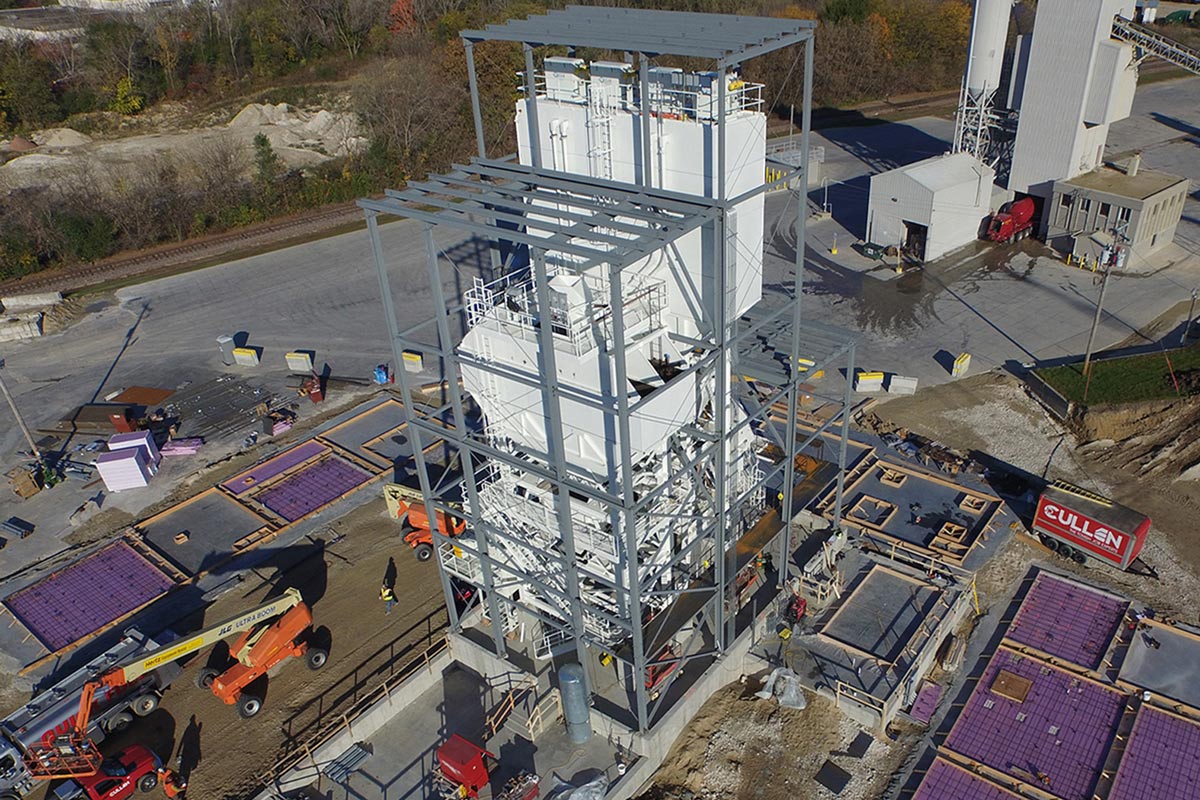
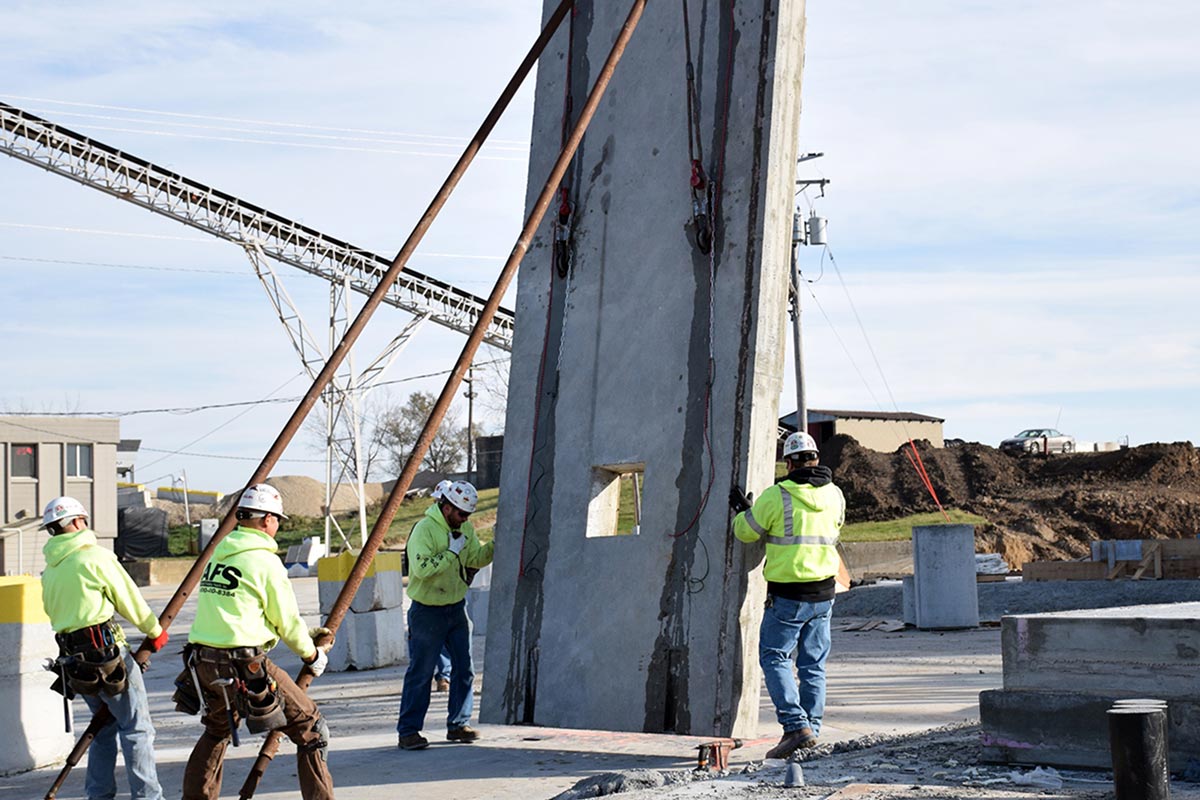
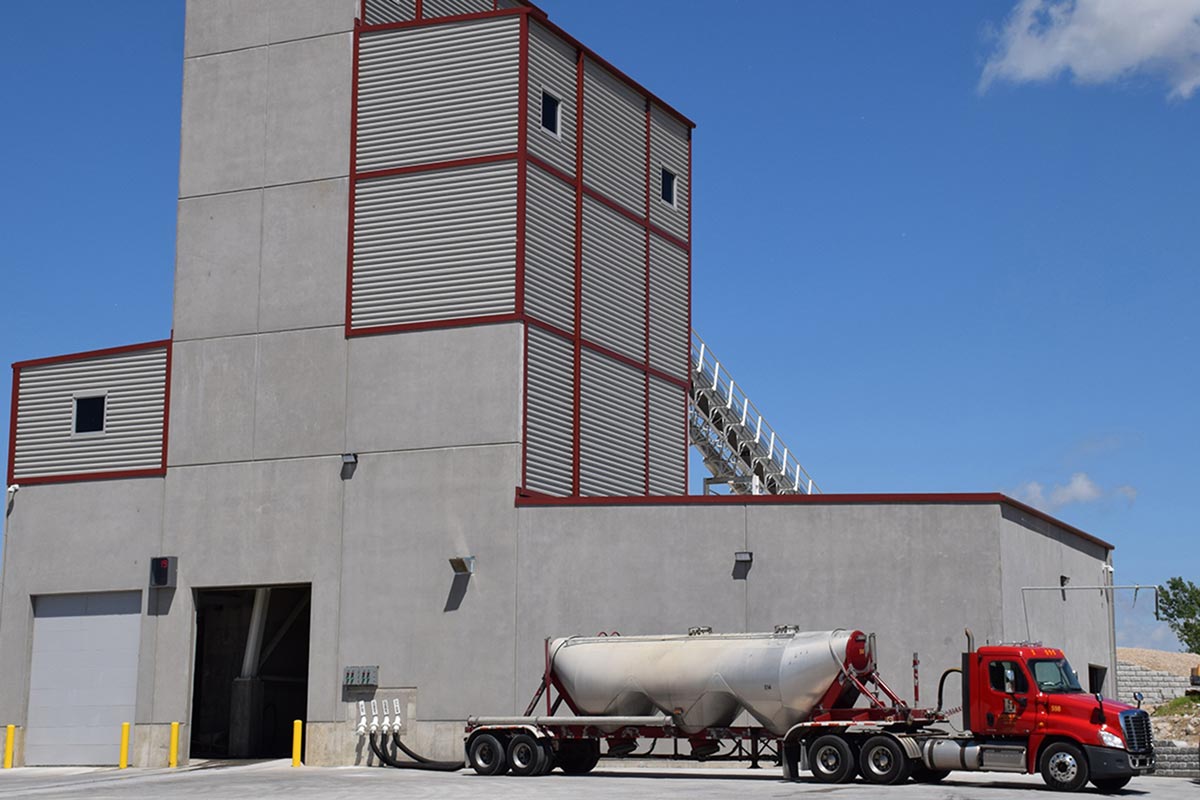
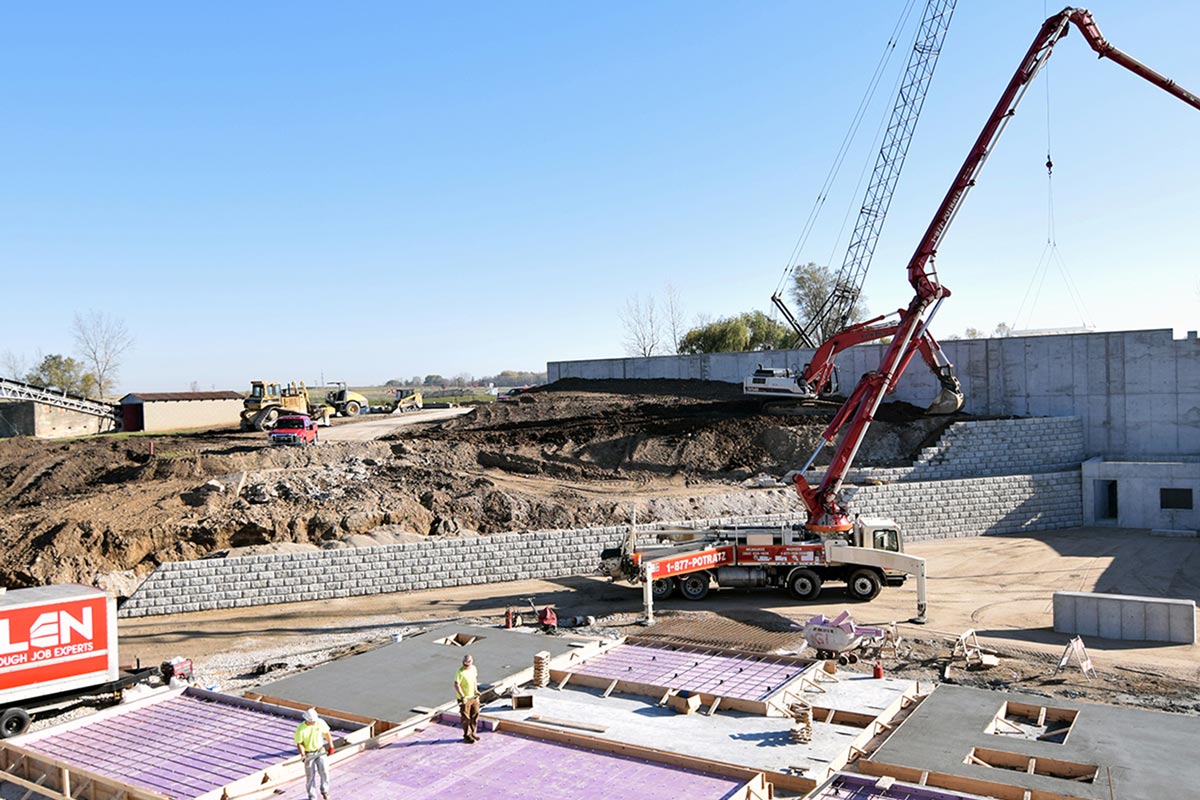
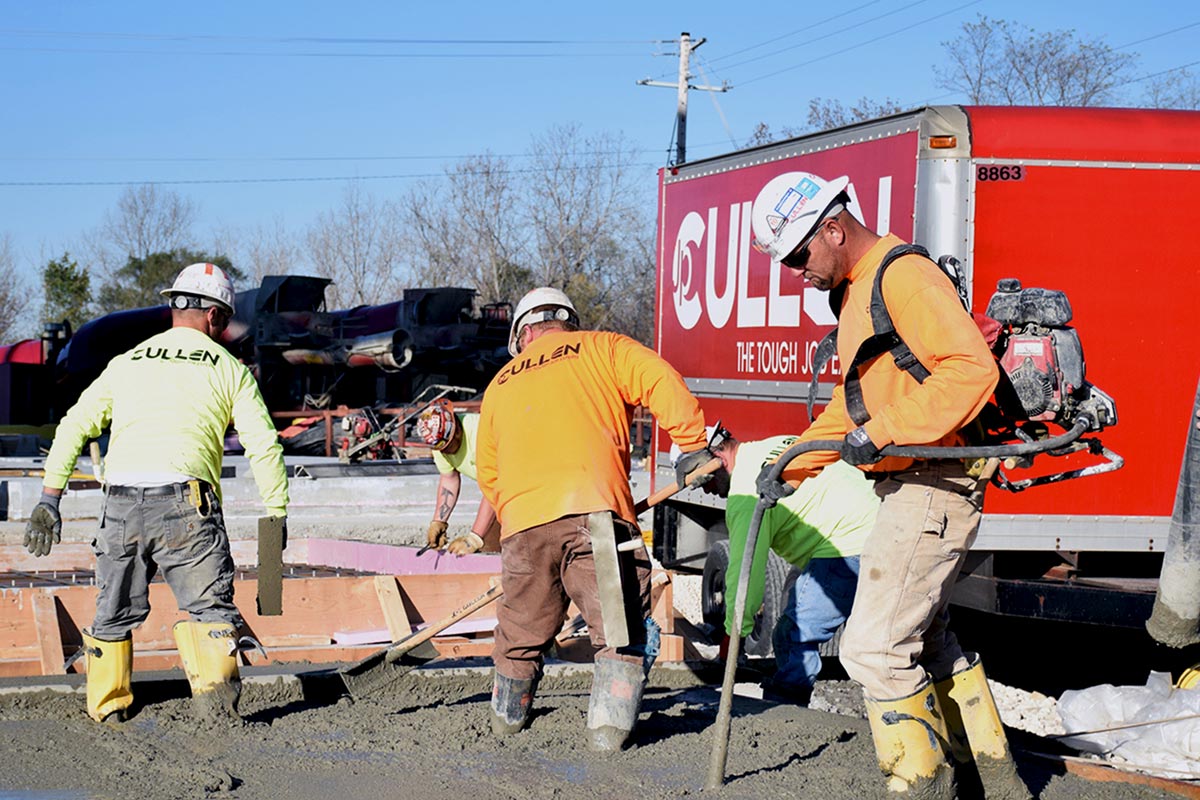
Size:
Location:
Teams:
This combined 10,400 square foot project consisted of a 2-story Concrete Batch Plant and a separate 3-story Aggregate Storage Facility. In order to save time and money, the two buildings were constructed using Tilt-Up panels. Find out how JP Cullen used Tilt-Up concrete to provide a unique solution to Lycon’s Concrete Batch Plant and Aggregate Storage Facility.
Both the steel-framed Batch Plant and Aggregate Storage Facility were originally designed to be constructed with precast panels, which had a six month lead me. This presented a problem since the owner wanted the Batch Plant operational in six months.
Through coordination between the owner, structural engineer, and general contractor, the decision was made to construct the buildings using Tilt-Up to save on cost and schedule.
This combined 10,400 square foot project consisted of a 2-story Concrete Batch Plant and a separate 3-story Aggregate Storage Facility. The two buildings contained 45 Tilt-Up panels, totaling roughly 17,400 gross square feet of insulated Tilt-Up panels. They were constructed using both stack-casting and conventional single high forming methods on sacrificial casting slabs and were formed, poured, and erected during the late fall/early winter months.
The Batch Plant building consisted of 29 unique panels, which were all different in either size, shape, embedded items, or openings. Nineteen of the 29 Batch Plant panels were attached to the supporting steel structure behind the concrete panel “cladding”. Because of this, those 19 panels were “Tilted” from the casting beds during erection and transferred mid-air to the edge, lifting inserts in the tops of the panels, allowing the panels to hang perfectly vertical and removing the rigging from the backs of the panels where there was only 1” of space between the steel structure and the back of the panels. The remaining panels on the Batch Plant and the 16 panels on the Aggregate Storage Building were set and temporarily braced until the roof structure was completed and the temporary bracing could be removed.
The Batch Plant also included an 88’-4 1/2” high tower to enclose the cement hopper, which was framed with five “stacked” Tilt-Up panels on two sides and a metal panel enclosure system on the adjoining sides. The bottom panel on the tower also included the largest opening on the building, which was a 14’ wide by 16’ high overhead door opening for concrete truck access. Due to the heavy load of the panels above, this opening required a custom bent plate jamb angle to frame the large opening in the structural wythe of the panel. Many of these panels contained architectural reveals and fascia wythe returns to eliminate exposed insulation at the ends of the panels.
The Aggregate Storage Facility panels made up the top 17’ ring of a 54’ tall overall structure, which was set on top of the cast-in-place bin walls below. A well thought out erection and bracing plan were required due to limited available bracing points and the bottoms of the panels being roughly 37’ in the air. The East elevation also contained six overhead door openings that were 12’-0” wide by 13’-11” high for aggregate truck access. Panels on both buildings were completed with a light sandblast finish to provide an aesthetic appearance.
By switching to Tilt-Up panels from precast panels, we were able to save the owner over $60,000 in project costs and improve the overall project schedule by three months. The Batch Plant was operational in six months, three months earlier when compared to previously constructed Batch Plants in the area.
We also eliminated approximately 90 loads of precast to the site. This resulted in less traffic on-site and reduced congestion, ultimately creating a safer work environment.
An additional sustainability benefit was the removal of emissions from delivery trucks. Since all work was done on-site, with an existing adjacent concrete batch plant, there was no need for a constant inflow of delivery trucks, as would have been required for precast panels.
JP Cullen was awarded the 2016 Tilt-Up Association Achievement Award Winner for this project.