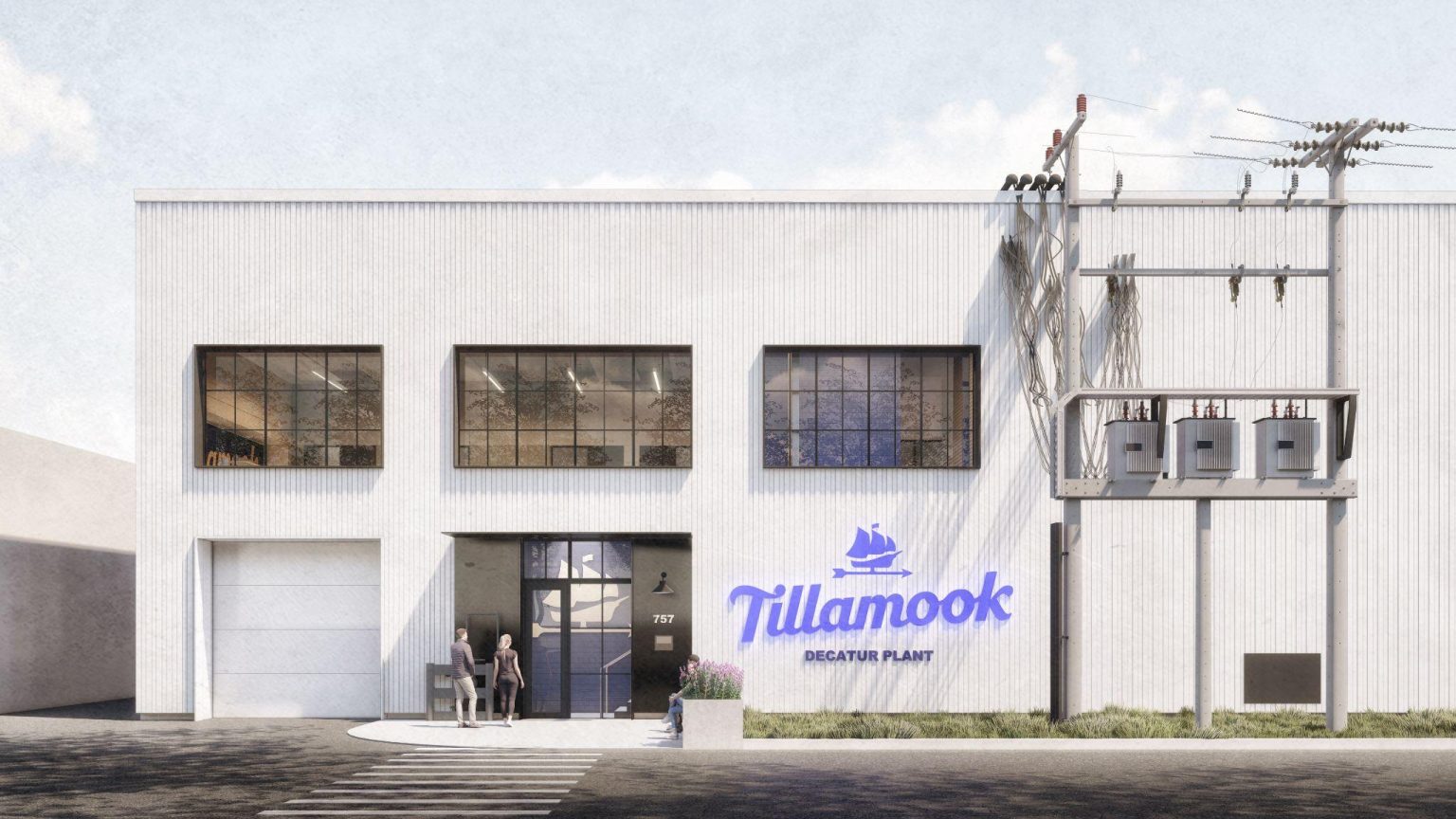
- Industrial
Tillamook New Ice Cream Production Facility
- Tillamook County Creamery Association
Location:
Overview:
JP Cullen took on the challenge of transforming Tillamook’s newly acquired facility in Decatur, Illinois—a former Prairie Farms factory built in the early 1900s—into a state-of-the-art production facility for their iconic ice cream.
With a complex scope and a tight schedule, our expertise in preconstruction and structural restoration was critical to the project’s success. The team navigated significant structural uncertainties and outdated infrastructure, ensuring the facility could support modern operational demands.
Challenges:
The project presented a series of unique challenges. The facility was originally built in the early 1900s, containing deteriorated materials and lacking modern structural reinforcements. There was an assumption made that since this was originally an ice cream facility, it would only require minimum upgrades to bring it back online.
Our initial engineering analysis uncovered key issues, including concrete strength concerns and absence of rebar. The site had no current drawings and relied on outdated plans, needing a comprehensive analysis and creative problem-solving.
Upon further investigation, it was determined that all utilities including power, water, and gas required extensive upgrades to meet current production needs. Unexpected complexities arose, including securing approval for new power lines extending into an adjacent property, which resulted in added scope under an already tight schedule.
Solutions
We conducted detailed assessments of the site’s structural integrity, including core sampling, rebar scanning, and laser scans of existing structures. These efforts provided a clear understanding of the building’s condition and informed critical decisions about restoration versus demolition. We provided expert recommendations, including the need for reinforcement strategies to ensure the building’s long-term stability, safety, and new equipment.
As design progressed, we provided multiple GMPs (Guaranteed Maximum Prices) throughout the evolving design process. Despite limited initial drawings, we consistently updated budgets based on design milestones, ensuring transparency and accuracy. The team had multiple design reviews. We continuously met to figure out how we could make this site work with the current site conditions and what new design elements were getting incorporated.
We led a rigorous value engineering process with Tillamook, identifying and presenting hundreds of cost-saving opportunities that balanced functionality and their company’s values for their facilities with budgetary needs. This included prioritizing quality and their dedication to their employees, such as employee spaces while looking for cost-saving opportunities.
Results:
Through our expertise and adaptability, we successfully overcame these challenges, delivering a modernized facility that met Tillamook’s operational needs. Structural reinforcements and utility upgrades ensured the facility could support production operations for years to come. We provided open book budget management, allowing Tillamook to effectively align its resources with key project goals.