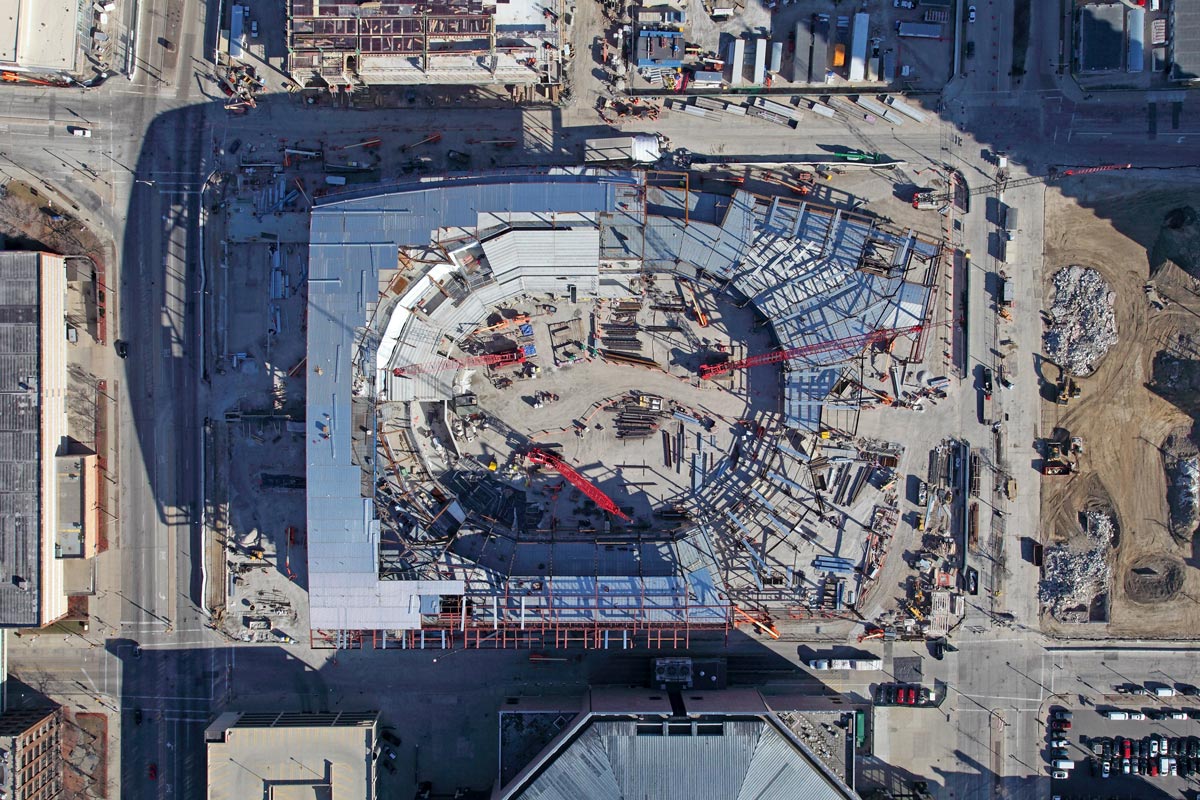
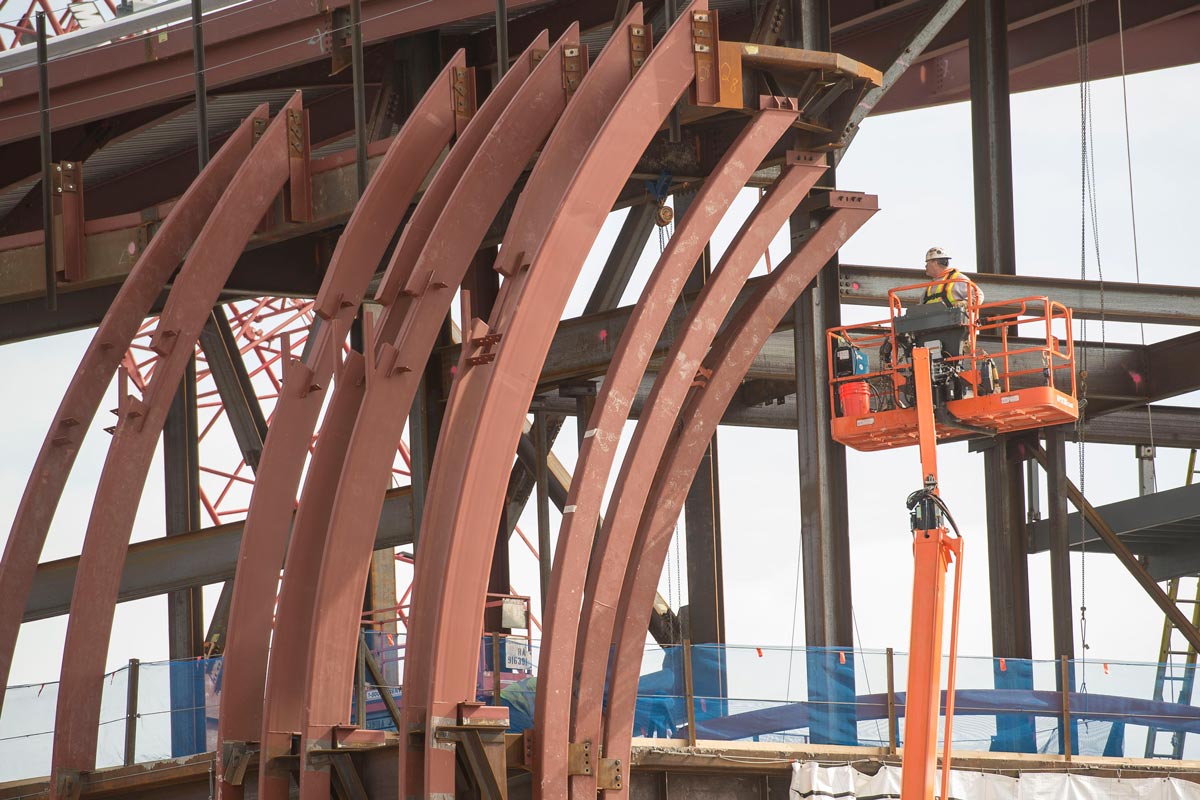
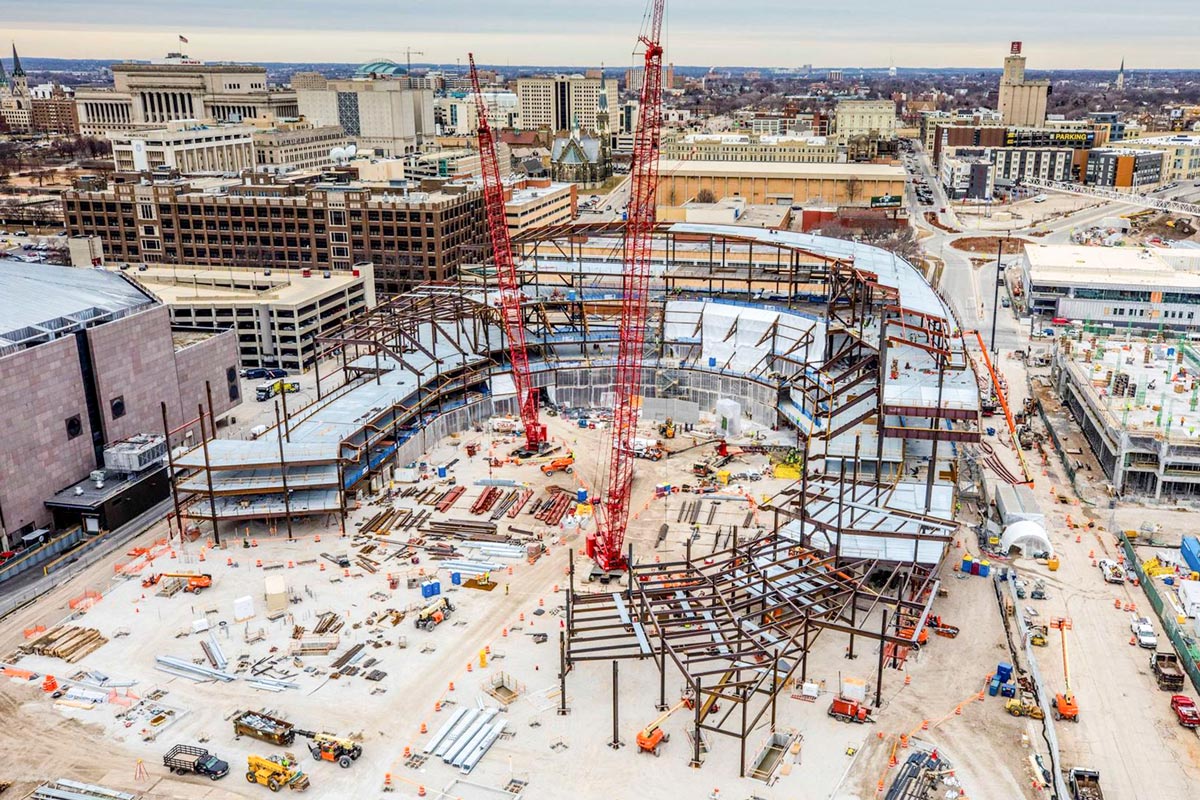
- Commercial, Industrial
Fiserv Forum Structural Steel
Size:
Location:
JP Cullen performed the steel erection for the new Milwaukee Bucks Arena. The total project consisted of approximately 8,000 tons of structural steel.
The steel construction consisted of typical structural column and beam steel framing for the surrounding bowl structure including 6 levels plus a roof. The roof over the arena floor consisted of 9 total long span roof trusses, approximately 33 feet deep, with the longest truss spanning 313 feet weighing 102 tons. The first piece of steel was set on November 7, 2016. Two hundred and ninety (290) days later, JP Cullen and the project team celebrated the “Topping Off”.
With the roof trusses being erected inside of the arena bowl, it made for tight quarters for all the crews, material, and equipment. These conditions could have adversely impacted the safety of tradespeople with this high-risk activity, as well as the laydown and work area for the crews. Extensive planning, sequencing, and coordination were necessary to ensure success.
Another challenge was the sequencing and delivery of the steel to keep the entire project on schedule. The steel schedule was critical to allow follow-up activities on the project. Creating a reliable fabrication and delivery schedule to maintain the supply of material needed to support the onsite erection operation was crucial.
Weather – including the wind speed – could become an issue if it shuts down the crane, thus impacting the schedule. If the anemometer on the crane measures the wind speed over 30 miles per hour, the lifting of the roof trusses would have to be stopped until it fell below the threshold.
This job was a high-risk activity that required a lot of planning from the very start. In fact, the team began preparing for this a year before. Planning included discussions on how the team was going to accomplish this process safely, what the site is going to look like, and what equipment the team needs on site.
This job was a high-risk activity that required a lot of planning from the very start. In fact, the team began preparing for this a year before. Planning included discussions on how the team was going to accomplish this process safely, what the site is going to look like, and what equipment the team needs on site.
This type of planning required engineering and the use of Building Information Modeling (BIM). BIM allowed the team to create a 3D model of the site long before this week for site planning, including details like where the cranes and truss rack should be placed. By the time the first truss arrived on site, the team had been preparing to set it for months.
The trusses came to the site as individual pieces, and the team used a truss rack to build the truss on the ground. Once assembled on the rack, the truss was erected. Two cranes were required to erect each truss half: the first crane picks and sets the actual truss, while the other crane is used to set infill steel (secondary trusses and beams) to stabilize the truss. The process of setting the half truss including all the secondary infill steel needed to stabilize the truss is a day-long process.
However, this process was much safer and more efficient than trying to build the truss piece by piece in the air. This would have taken weeks and introduced many safety concerns that were eliminated by the process of assembling each truss on the ground.
The project began in November of 2016 and was topped out on August 24, 2017. A job of this size required detailed safety, quality, and erection plans. JP Cullen worked with Mortenson, the CM (Construction Management), and Merrill Steel, the fabricator, as early as (8) months before steel erection to develop sequences and schedule. JP Cullen’s dedication to safety, pre-planning, teamwork, and coordination proved to be successful as the project finished (3) weeks early.