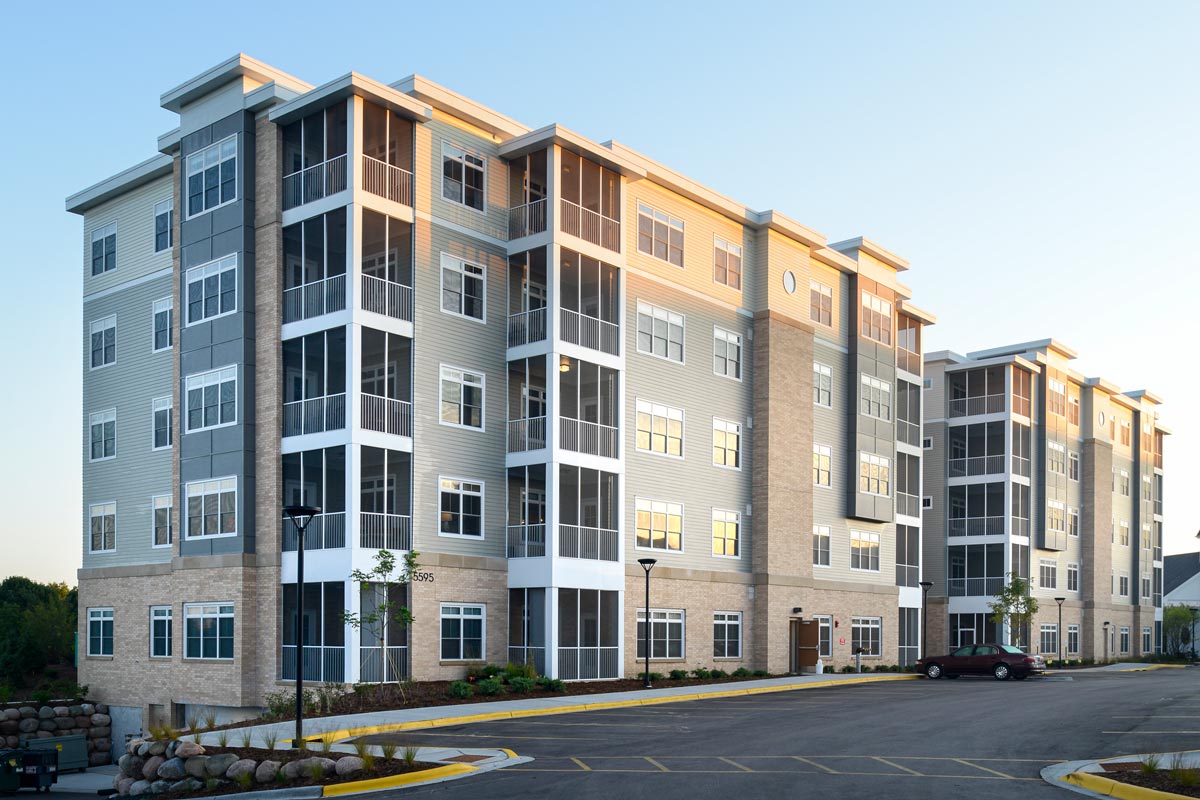
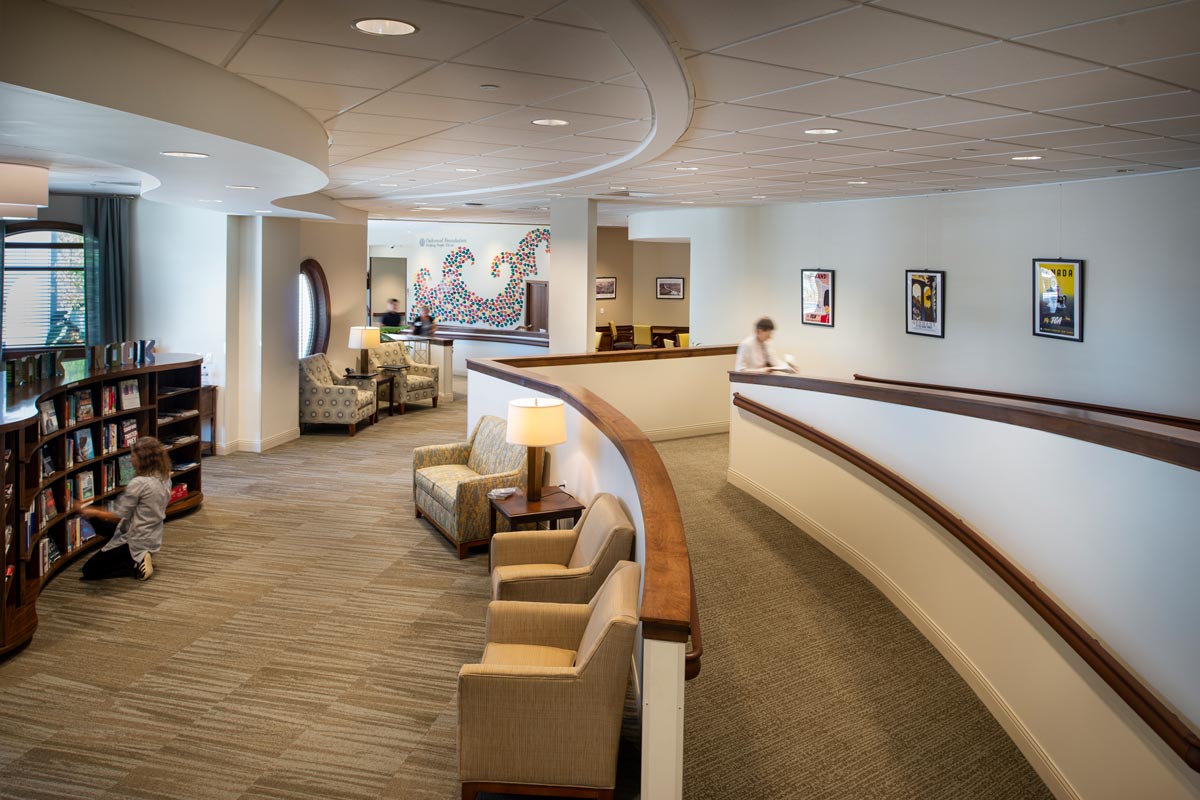
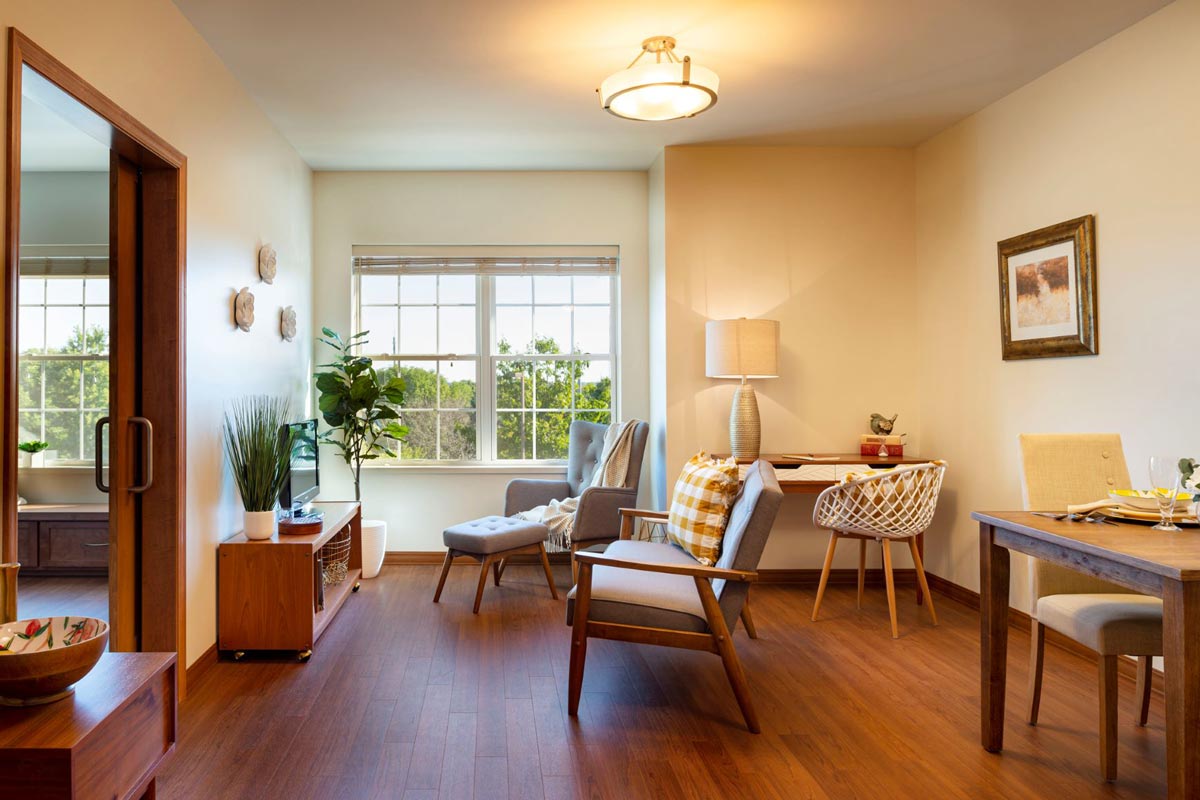
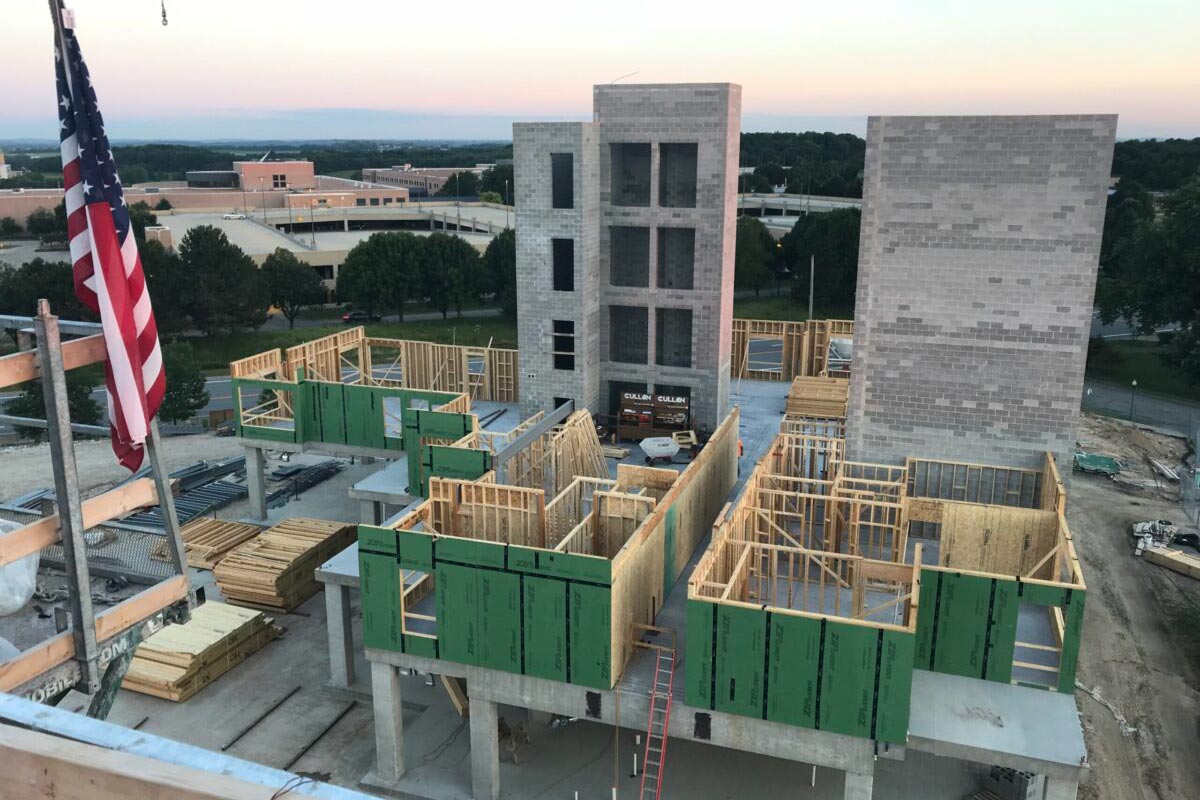
- Healthcare
Oakwood Village Prairie Ridge Campus Project
Square Footage:
Location:
Oakwood Village, the largest retirement organization in Madison, was continuing to see demand for high-quality housing and services and anticipated that would continue to grow as baby boomers entered their retirement years.
To meet this demand and their growing wait list, they constructed three, five-story towers built over structured parking for the addition of 73 new independent living apartments. An expansion to the existing assisted living entry care facility included construction of a three-story building for 30 more one-bedroom apartments, support spaces and common areas.
Renovations to existing common areas were focused on offering amenities to match the evolving interests of a new generation of retirees. It included pub and bistro food service venues, community center enhancements, a lifelong learning center, modern fitness spaces, art galleries, the chapel and a new space for the creation of a spa.
The project had to fit within Oakwood’s budget cost model parameters, so JP Cullen was brought on board early to provide cost estimating services, design input, constructability analysis, formal budgeting at each design phase and GMP development. With the primary architect located in Virginia, we also ensured the project adhered to Wisconsin codes and standards. The mechanical, electrical, plumbing and fire protection subcontractors were also brought on board on a design-assist basis to provide input on design, value alternatives and constructability. All of these efforts helped to ensure that the project did not exceed their cost model for the units.
A state-wide building boom resulted in a labor shortage and limited manpower. Having started the operation two weeks behind goal, prefabrication was key to make up for lost time and get the schedule back on track. Crew members needed to be assigned to other portions of the building to keep the schedule moving.
Three towers needed to be assembled simultaneously which created a tight timeline from the start. Upfront coordination with the wood framing supplier was critical and communicating how JP Cullen planned to sequence the assembly of the towers. Sequencing was determined by move in date of the tenants. There was a two-week period between the start of each tower.
Prefabrication of the three towers included 2,404 wood joists, 355 headers, 2,616 wood frames, 3,267 floor trusses and 114 roof trusses. The prefabrication of these components got the schedule back on track to complete on time and made up for the two weeks that were lost.
Prefabricating portions of this project resulted in 10% cost savings and 25% schedule savings.